How An Ultrasonic Works ?




Ultrasonic cleaners are unsurpassed when it comes to removing contaminants from virtually any hard surface that can be safely immersed in a cleaning solution.
Ultrasonic cleaners are fitted with transducers attached to the bottom of a tank filled with cleaning solution. Transducers create vibrations at high frequencies measured in thousands of cycles per second (kHz) and send sound waves through the cleaning solution. These waves produce millions of tiny vacuum-filled bubbles that shoot out powerful jets of liquid when they implode. The force of the implosions, called cavitation action, lifts contaminants off the objects being cleaned. The process is tough enough for carburetors but gentle enough for electronics and surgical instruments.
Our Technology
1) SS Basket
​
2) 316-L, 2MM Thickness Stainless Steel.
​
3) True Sweep Frequency Generator.
​
4) Stainless Steel Top Lid.
​
5) Digital Controls.
​
6)Stainless Steel Frame.

Sweep Frequency
The True Sweep frequency mode in our Ultrasonic Generators allows a constant fixed slight variation in the ultrasonic frequency around the resonant frequency. Such operation of the generator allows uniform cleaning thereby avoiding some problems in the old traditional generators which cause standing waves to not only damage the parts but also promote inferior cleaning.

With the all new sweep frequency, we not only ensure that the parts are cleaned more evenly but also the shelf life of the working tanks is enhanced as compared to the traditional ultrasonic generators.Our generators are proven to perform a greater cleaning level due to the uniform acoustic field distribution in the ultrasonic tank.
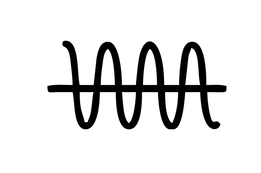
How to Choose An Ultrasonic Cleaner ?
1)Purpose of Ultrasonic Cleaner:
An Ultrasonic cleaner can do much more than just cleaning parts. It is used to degas solvents, disperse nanoparticles, emulsify & dissolve solvents as well as it is used in preparing lab samples. If your primary purpose is to clean parts, then you need to clearly define the size and weight of the parts, type of contamination and the cleanliness criteria that you are seeking.

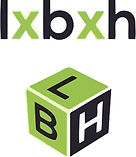
2) Size of the components to be cleaned:
Measure the dimensions of largest parts to be cleaned and make sure to select a tank that will accommodate these parts. In addition, pay attention to the internal dimensions of the parts basket, since this is most likely where you will put the parts during cleaning.
3) Material Handling Basket:
Baskets are used to support parts in an ultrasonic cleaner. They affect cleaning efficiency and the life of the tank. Baskets with insulated handles facilitate placing and removing parts being cleaned in hot liquid. They also keep parts of the tank bottom where they suppress vibration and lower cleaning effectiveness.


4) Heating element in the tank:
Most cleaning operations are much more effective with heating. It's a lot like doing laundry. A hot cleaning solution is best for removing oils, machining coolants and a whole host of other contaminants from just about any surface one can think of. Although heat is a natural by-product of ultrasonic cavitation, cleaning efficiency increases when you give it a boost by using ultrasonic cleaners with thermostat- controlled heaters.
5) Sweep Mode Operation:
We're not talking about brooms here. Sweep mode is a small continuous variation of the ultrasonic frequency around a central value, such as 40 kHz±3 kHz. When an ultrasonic cleaner operates at a fixed frequency without Sweep there are three potential problems: hot spots, dead zones and harmonic vibrations. Select a unit with a Sweep mode such as the Transonic's models if you are cleaning precision parts and surgical instruments when highly uniform cleaning is needed.


6) Choose correct Ultrasonic Frequency:
Most ultrasonic cleaners operate between 28 and 40 kHz.This frequency range is well suited to the vast majority of cleaning tasks. A lower frequency such as 28 kHz produces larger cavitation bubbles. When these bubbles implode they release a larger amount of cleaning energy. For coarse cleaning such as removal of lapping abrasives or polishing paste, a lower frequency will be more effective. A higher frequency produces smaller cavitation bubbles. These cover fine featured complex surfaces more thoroughly and are more gentle than low frequencies.
7)Do you need Degas mode?
If you are cleaning parts, keep in mind that every time you fill the tank with a fresh cleaning solution you must degas by switching on the generator for 5-10 minutes before the unit can clean effectively, A Degas mode will enable you to start cleaning soon after you fill the tank. It does the job by switching on and off causing air bubbles to coalesce and allowing them to rise to the surface and burst.Pulse mode provides intermittent spikes of very high ultrasonic power to remove stubborn contaminants. Pulse mode also degasses solutions very effectively.


8)Cleaning Chemical:
The correct cleaning solution chemistry is as important as ultrasonic frequency, power and other points covered in this selection guide. You should contact R. K. Transonic Engineers Pvt. Ltd. for detailed information on the correct formulation for your jobs. Most commonly used chemistries fall into three categories: alkaline, acidic and neutral. They are usually supplied as concentrates so a little goes a long way. Their non-toxic biodegradable chemistry eases disposal concerns.